Health and Safety Culture at Workplace | How to Create a Safer Workplace
Building a strong health and safety culture isn’t just a legal checkbox, it’s the heartbeat of any organization striving for zero incidents and maximum productivity. Organizations with a positive safety culture empower employees to actively participate in risk reduction, driving down injury rates and boosting morale HSE. By embedding safety into everyday decision‑making, companies unlock long‑term benefits: fewer disruptions, enhanced reputation, and lower insurance costs.
In this post, we’ll explore five foundational HSE (Health, Safety & Environment) best practices—grounded in global standards and real‑world success stories—that will help you create a safer workplace from the ground up.
Understanding HSE Standards Fundamentals for Health and Safety Culture at Workplace
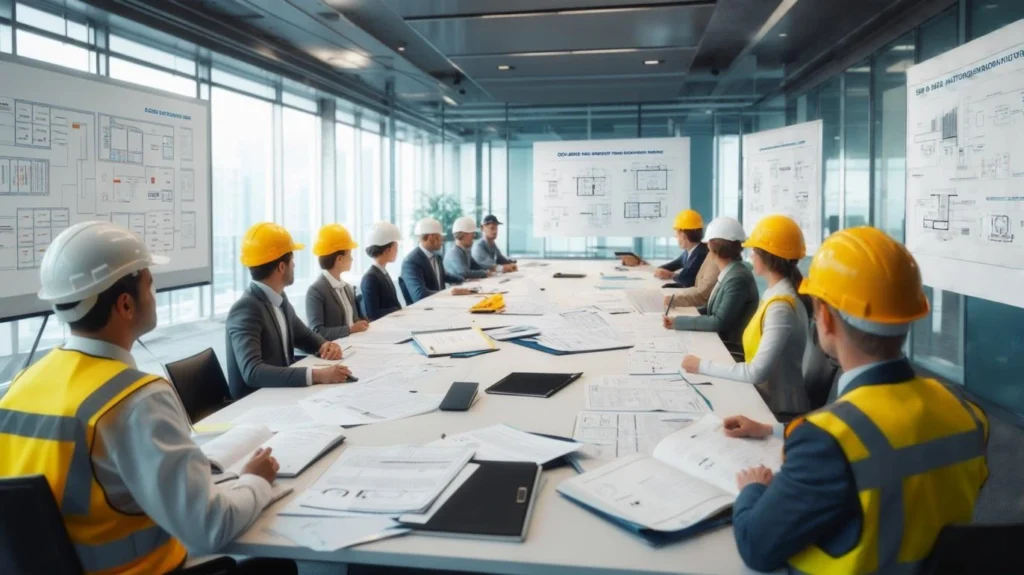
What HSE Standards Encompass and Why They Matter
HSE standards provide a framework for identifying hazards, implementing controls, and continuously improving workplace safety. At their core, they aim to:
- Prevent work‑related injuries and illnesses
- Protect the environment from release of harmful substances
- Ensure legal and ethical compliance
Adhering to standards like ISO 45001 (the international benchmark for occupational health and safety) not only demonstrates due diligence, but also helps organizations systematize risk management in a scalable way SafetyCulture.
Key Regulatory Bodies Governing HSE Standards Globally
- Health and Safety Executive (HSE) (UK): The independent regulator for work‑related health, safety, and illness, established under the Health and Safety at Work etc. Act 1974 Wikipedia.
- Occupational Safety and Health Administration (OSHA) (USA): Sets and enforces standards to ensure safe work environments under the OSH Act of 1970 OSHA.
- International Labour Organization (ILO): Publishes conventions and recommendations that influence national legislation worldwide.
Evolution of HSE Standards Over the Decades
Over the past 50 years, HSE has evolved from simple checklist compliance towards comprehensive management systems emphasizing:
- Leadership commitment
- Worker participation
- Risk‑based thinking
- Continuous improvement
This progression reflects a shift from reactive “bolt‑on” safety measures to proactive safety cultures where every employee feels empowered to speak up and intervene.
Core Components of Effective HSE Standards
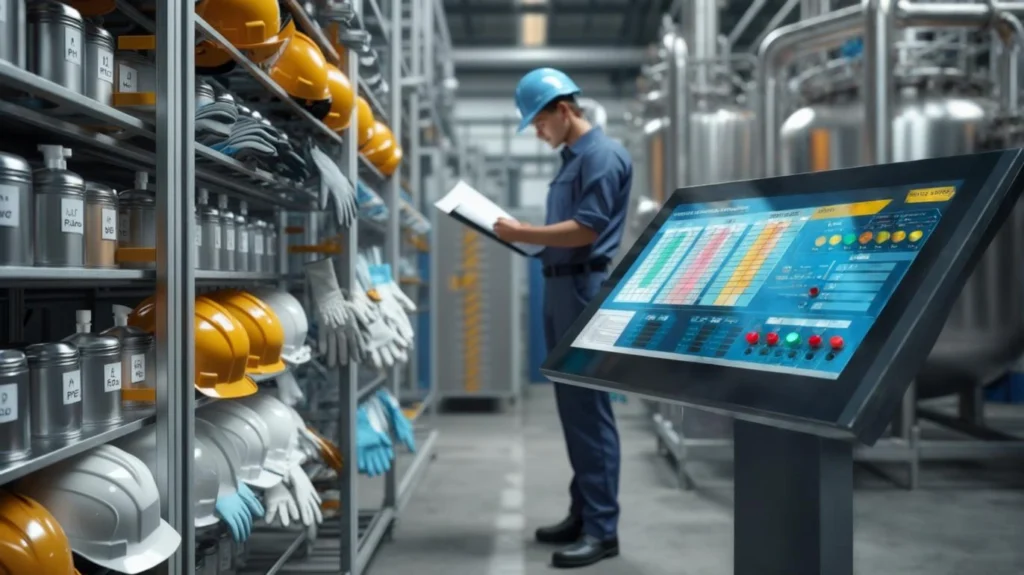
Risk Assessment Frameworks That Protect Organizations
A robust risk assessment process is the cornerstone of any HSE program. Key steps include:
- Hazard Identification: Gathering information from audits, incident reports, and worker feedback OSHA.
- Risk Analysis: Evaluating severity and likelihood to prioritize controls OSHA.
- Risk Control: Applying the hierarchy of controls—from elimination and substitution to engineering and administrative measures.
Embedding regular risk assessments into operations ensures emerging hazards are promptly addressed, not left to fester until an incident occurs.
Safety Management Systems and Implementation Protocols
Implementing an OHS management system (as per ISO 45001) involves:
- Establishing a clear HSE policy endorsed by top management
- Defining roles, responsibilities, and accountabilities
- Integrating HSE objectives into business planning
- Conducting internal audits and management reviews
By aligning safety goals with business objectives, organizations reinforce that safety is a strategic priority, not an afterthought www.assp.org.
Environmental Protection Measures
Modern HSE programs extend beyond worker safety to environmental stewardship:
- Pollution prevention: Waste reduction, spill containment, and emissions controls
- Sustainable resource use: Energy efficiency and circular economy practices
- Environmental monitoring: Regular sampling and impact assessments
Coupling health and safety initiatives with environmental goals creates a holistic EHS (Environment, Health & Safety) approach that resonates with stakeholders and regulators alike.
Occupational Health Considerations
Protecting worker health requires addressing:
- Ergonomics: Designing workstations to reduce musculoskeletal disorders
- Wellness programs: Mental health support, stress management, and fitness incentives
- Exposure controls: Monitoring and reducing exposure to noise, chemicals, and dust
Prioritizing occupational health fosters well‑being, reduces absenteeism, and improves employee engagement.
Implementing HSE Standards in Your Organization
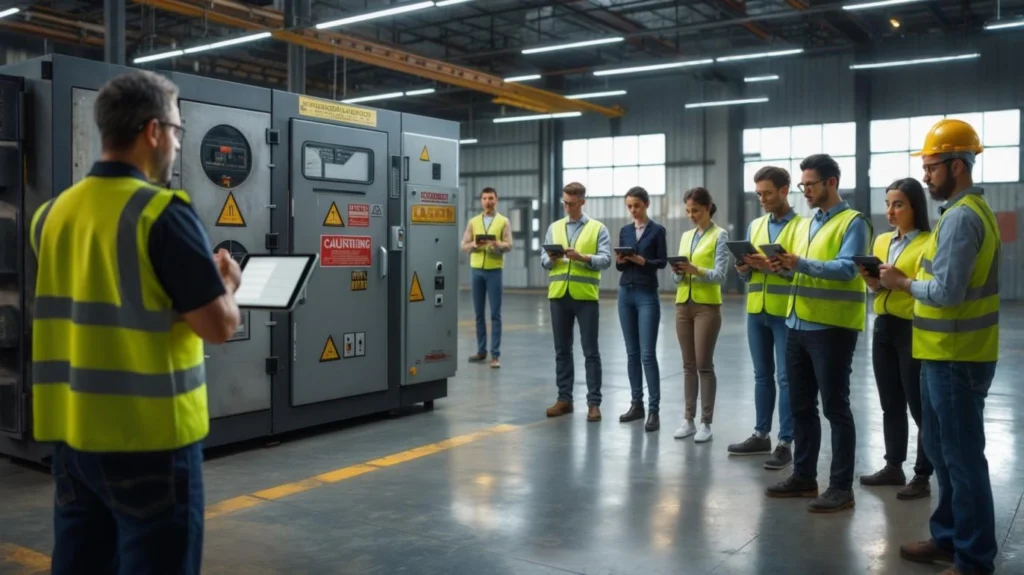
Gap Analysis: Identifying Compliance Shortfalls
A structured gap analysis compares your current practices against international benchmarks (e.g., ISO 45001, OSHA Recommended Practices). Steps include:
- Document review: Policies, procedures, and records
- Site audits: Walk‑around inspections and worker interviews
- Data analysis: Incident trends and near‑miss reports
This systematic approach uncovers hidden vulnerabilities and informs targeted action plans.
Creating HSE Policies Aligned with International Standards
Craft policies that are:
- Clear and concise: Avoid jargon; use plain language
- Risk‑based: Focus on identified high‑risk areas first
- Accessible: Ensure policies are available in print and digitally
Link your policies to standards directly—e.g., “Our respiratory protection program meets ISO 45001:2018 clause 8.1” or “We comply with OSHA’s General Duty Clause” OSHA—to demonstrate alignment and ease audits.
Training Programs That Drive Behavioral Change
Effective training goes beyond slide decks:
- Scenario‑based learning: Simulations and role plays that mirror real hazards
- Micro‑learning modules: Short, focused bursts delivered via mobile apps
- Peer‑to‑peer coaching: Senior workers mentoring new hires
By reinforcing training with on‑the‑job coaching and regular refresher sessions, you cultivate a workforce that instinctively applies safe behaviors.
Documentation and Record‑Keeping Best Practices
Maintain accurate, up‑to‑date records of:
- Risk assessments and control measures
- Training attendance and competencies
- Incident investigations and corrective actions
- Equipment inspections and maintenance logs
Well‑organized documentation supports due diligence and accelerates investigations when incidents occur.
Technology Solutions for HSE Management
Leverage digital tools to streamline HSE processes:
- EHS software platforms: Centralize incident reporting, audit management, and dashboarding
- Mobile inspection apps: Enable real‑time hazard reporting with photos, GPS, and electronic signatures
- Wearable sensors: Monitor worker location, vital signs, and environmental conditions in high‑risk zones
Integrating technology not only improves data accuracy but also enhances visibility for leadership.
Industry‑Specific HSE Requirements
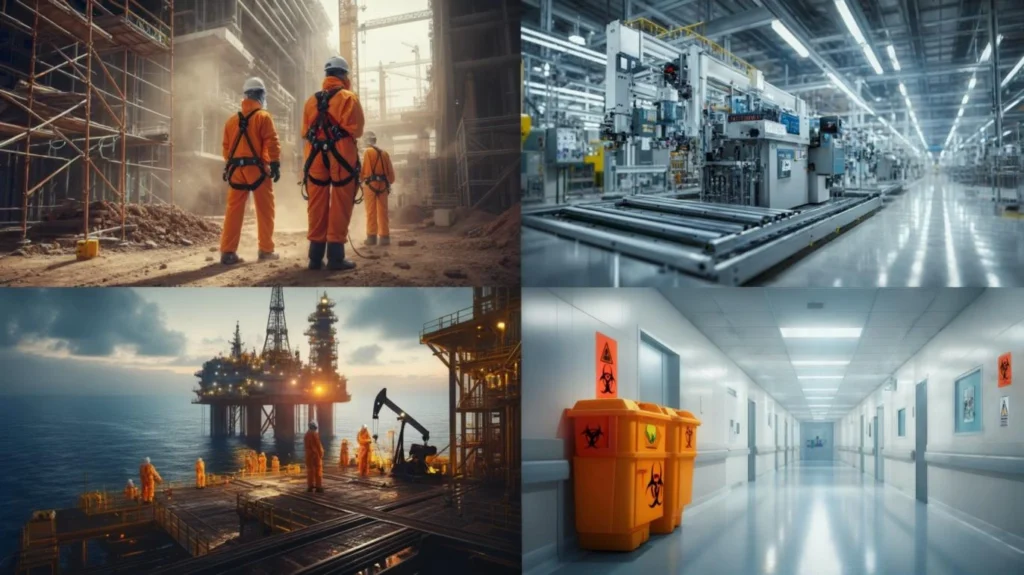
“No two industries are identical—tailor your HSE approach to your sector’s unique risks.”
Construction Sector HSE Critical Controls
- Permit‑to‑Work systems for hot work, confined spaces, and high‑risk activities
- Fall protection measures: Guardrails, harnesses, and safety nets
- Equipment inspection protocols: Daily pre‑use checks for cranes, scaffolds, and heavy machinery
For deeper insights, see our Comprehensive Crane Operation Safety Guide.
Manufacturing Safety Protocols
- Lockout/Tagout (LOTO): Strict control of hazardous energy sources during maintenance Wikipedia.
- Machine guarding: Fixed and interlocked guards on moving parts
- Chemical safety: Proper storage, labeling, and handling of hazardous substances
Oil and Gas Industry Specialized Standards
- Process Safety Management (PSM): As mandated by OSHA 29 CFR §1910.119, covering PHA, MOC, and emergency planning Wikipedia.
- Barrier management: Ensuring layers of protection function as designed
- Environmental monitoring: Leak detection and air quality surveillance
Healthcare Facility Safety Considerations
- Sharps and biohazard management: Safe disposal and immunization programs
- Ergonomic patient handling: Mechanical lifts and transfer aids
- Infection control protocols: PPE usage, hand hygiene, and isolation procedures
Measuring HSE Performance
Leading vs. Lagging Indicators Explained
Indicator Type | Purpose | Examples |
Lagging | Reflect past performance; reactive | Recordable Incident Rate (RIR), lost-time injuries |
Leading | Predict future performance; proactive | Number of safety observations, near-miss reports |
Focusing on leading indicators drives proactive interventions before incidents occur.
Developing Meaningful HSE Metrics
- Total Recordable Incident Rate (TRIR): Measure severity and frequency of incidents.
- Corrective Action Closure Rate: Track resolution speed of audit findings.
- Training Effectiveness Score: Assess knowledge retention via quizzes or on‑the‑job assessments.
Well‑chosen metrics align with organizational goals, enabling clear performance tracking and accountability.
Incident Investigation and Root Cause Analysis
When incidents do happen, a rigorous investigation is essential:
- Collect evidence: Photos, witness statements, and equipment logs
- Analyse root causes: Use methodologies like 5 Whys or HAZOP
- Implement corrective actions: Address systemic gaps, not just surface issues
Document lessons learned and share them across teams to prevent recurrence.
Continuous Improvement Methodologies
Adopt proven frameworks such as:
- Plan-Do-Check-Act (PDCA): Embed iterative cycles of improvement.
- Kaizen: Engage frontline workers in small, incremental safety enhancements.
- Six Sigma: Use data‑driven techniques to reduce variability in safety processes.
Continuous improvement cements safety as a living process, not a one‑time project.
The Business Case for Strong HSE Standards
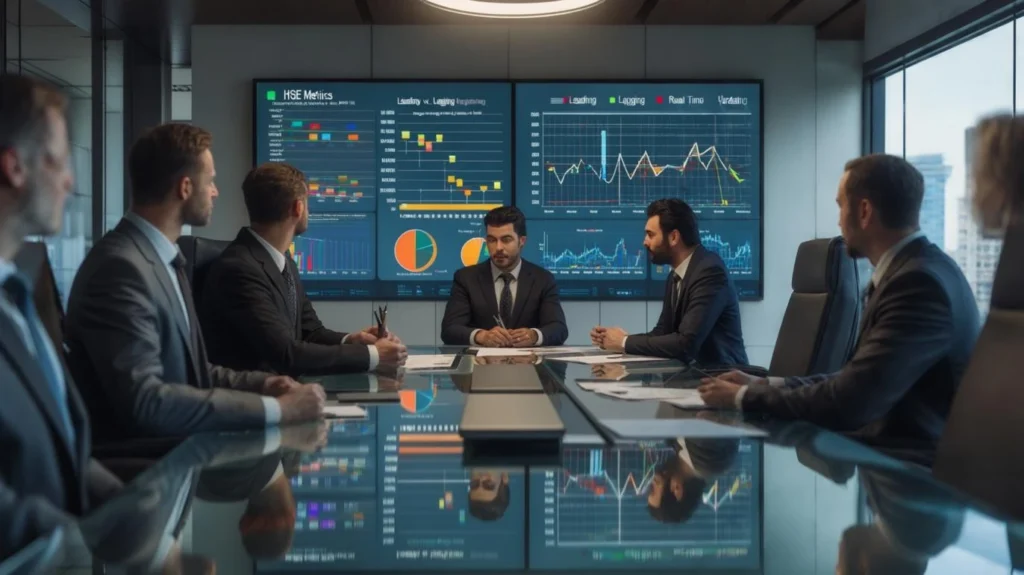
Cost Benefits of Effective HSE Implementation
- Reduced insurance premiums: Lower incident rates drive down risk profiles.
- Fewer shutdowns: Minimize costly downtime due to accidents or environmental incidents.
- Lower workers’ compensation claims: Tangible savings realized each year.
According to the ILO, every dollar invested in occupational safety yields a return of up to $4.50 in reduced costs LinkedIn.
Reputation Management and Stakeholder Confidence
A strong safety record builds trust with clients, regulators, and the public. Companies known for excellence in HSE:
- Win more contracts
- Attract ESG (Environmental, Social, Governance) investors
- Enhance brand loyalty among customers
Legal Protection and Liability Reduction
Compliance with HSE standards mitigates legal risk:
- Demonstrates due diligence in court
- Reduces fines and penalties from regulators
- Supports stronger defense in liability claims
Employee Retention and Productivity Advantages
Workers value employers who prioritize their well‑being:
- Higher morale and engagement
- Lower turnover rates
- Increased productivity and quality of work
Investing in health and safety is, at its core, an investment in people—and people power performance.
Conclusion & Call‑to‑Action
Creating a safer workplace demands a holistic approach: from grasping HSE fundamentals to deploying cutting‑edge technology and measuring performance with the right metrics. By championing these five best practices—standards comprehension, core component mastery, strategic implementation, industry tailoring, and rigorous measurement—you’ll forge a health and safety culture that not only saves lives but also drives business success.
What’s Your Next Step?
➡ Share Your Insights: Which of these practices resonates most with your organization? Drop a comment below!
Together, let’s build workplaces where safety isn’t a department—it’s a way of life.