Standard OSHA Crane Inspection Requirements
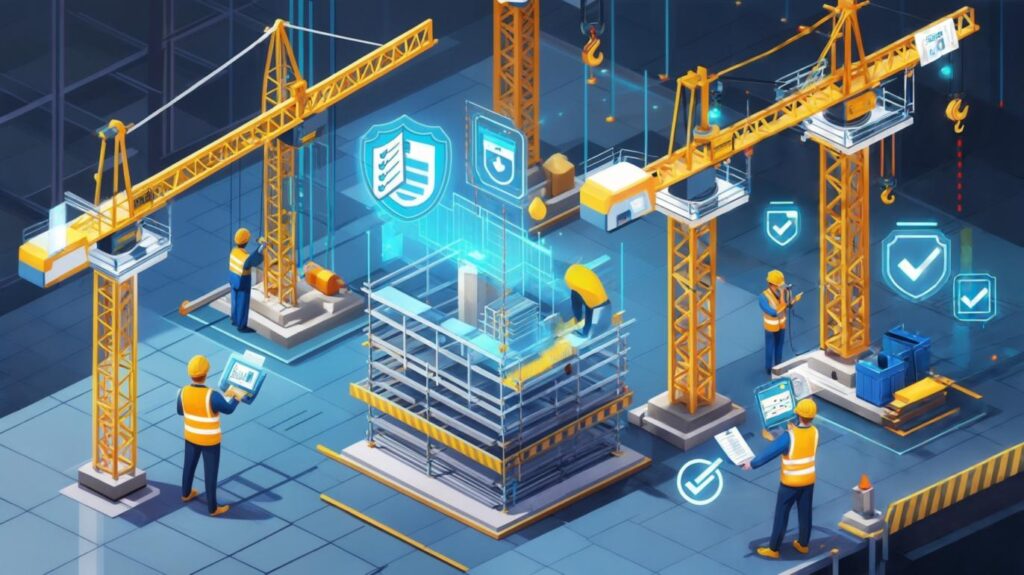
Imagine starting your workday on a bustling construction site, crane roaring to life, and knowing that every hook, wire rope, and control mechanism has passed rigorous checks. Welcome to the world of Crane Inspection Requirements, where safety is non-negotiable. Whether you’re managing a fleet of overhead cranes in a warehouse or overseeing derricks on a high-rise build, understanding OSHA’s inspection mandates is crucial—not just for compliance, but for protecting lives and assets.
From my years of experience working alongside heavy machinery, I’ve seen firsthand how crane inspection requirements can either make or break a job site’s safety culture. It’s not just about ticking boxes—it’s about avoiding breakdowns, preventing injuries, and making sure everything runs smoothly day after day. When heavy lifting and material handling are part of your routine, the safety and reliability of the equipment you rely on become non-negotiable. A well-maintained crane doesn’t just protect your people—it protects your bottom line.
Following OSHA’s standards is crucial. There are two types of inspections you need to keep in mind: frequent and periodic. Frequent inspections happen at daily, weekly, or monthly intervals. These cover the basic function, operation, and performance of the crane to catch anything unusual early on. Then come the periodic ones—scheduled bimonthly, quarterly, or even yearly—where deeper checks look for wear, hidden issues, and equipment integrity. Based on my experience, skipping either type has only led to trouble—whether it’s accidents, expensive fixes, or delayed projects.
Whether you’re in Construction, Manufacturing, or Mining, sticking to the proper regulations helps avoid expensive fines and boosts on-site efficiency. Crane inspection requirements aren’t just legal checklists—they’re practical steps that help you operate safely and minimize the risk of failure. And if you’re aiming to meet third party crane inspection requirements, everything needs to be up to code. Complying with these expectations ensures you’re not just protecting your team but also your company’s reputation.
In short, regular testing and timely maintenance aren’t just part of a compliance routine—they’re about building a work environment where people trust the machines they’re using. After all, a proactive approach to crane inspection requirements means fewer surprises, more confidence, and a lot more peace of mind on the job.
Understanding OSHA Crane Inspection Rules from the Ground Up
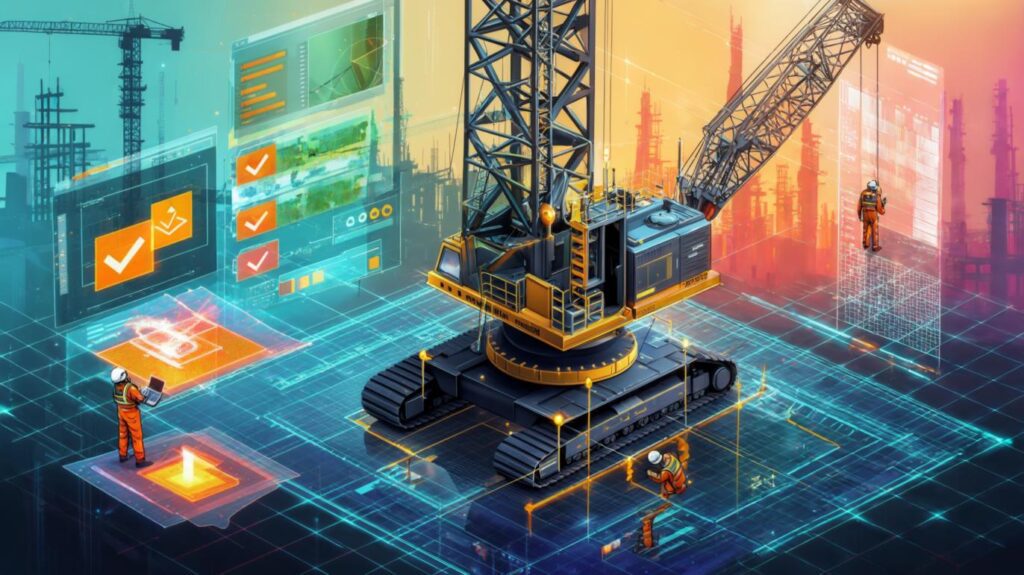
When I first started working around cranes, I didn’t realize how detailed the crane inspection requirements were until I had to follow them to the letter on a busy construction site. What I learned is that the OSHA rules aren’t just paperwork they’re essential for preventing real accidents. Under 29 CFR 1910.179, inspections for overhead and gantry cranes in general industry must follow specific frequencies and procedures to ensure equipment is always safe to use. These standards set expectations not just for daily operations but for long-term maintenance, detailed testing, and design integrity.
In my experience, ignoring inspection details or missing a single step in a procedure can lead to dangerous consequences. That’s why the regulations outlined in 29 CFR 1910.180 for crawler, locomotive, and truck cranes are so strict. They focus on load handling, inspection, and maintenance to keep these massive machines stable in any condition. Every crane, whether it’s rolling across a factory or parked on a job site, needs to be up to OSHA’s requirements before a single lift is made.
Some companies choose to bring in experts for third party crane inspection requirements, especially when managing rigging equipment or doing complex lifts. For those cases, 29 CFR 1926.251 becomes critical. It applies to material handling, including slings, shackles, and all rigging gear, demanding thorough inspection, correct usage, and reliable maintenance. These standards make sure everything connected to the crane is just as trustworthy as the crane itself.
In our warehouse, where derricks are sometimes used, 29 CFR 1910.181 reminds us how a boom pivoted at its base can create hidden stress points. That’s why routine inspection and ongoing maintenance are non-negotiable. Even components not directly on the crane, like slings covered under 29 CFR 1910.184, play a huge role in lifting operations safely. If it lifts, it must be checked—and that’s a rule I live by.
Construction vs. General Industry: A Comparative Overview
OSHA divides crane inspection rules between the Cranes and Derricks in Construction Standard (29 CFR 1926.1412) and the Overhead & Gantry Cranes Standard for general industry (29 CFR 1910.179). Below is a quick reference to help you navigate the key differences:
Inspection Type | Construction (1926.1412) | General Industry (1910.179) |
---|---|---|
Shift Inspections | Visual pre-shift inspection by a competent person OSHA | Not specifically required; rely on frequent/periodic inspections as defined by ANSI B30.2 OSHA |
Monthly Inspections | Documented monthly inspection by a competent person OSHA | Complete inspection at intervals based on activity, severity, environment OSHA |
Annual Inspections | Comprehensive inspection “at least every 12 months” by a qualified person OSHA | “Complete inspections…at intervals as generally defined” by ANSI B30.2 OSHA |
Post-Assembly & Modified Equipment | Required before initial use and after substantial modification OSHA | Treated as a “new” crane; must meet ANSI testing requirements before use OSHA |
Documentation | Must retain inspection records for the life of the equipment OSHA | Certification records required for hooks & hoist chains; intervals noted in 1910.179(j)(2) OSHA |
Key Insights into OSHA’s Crane Inspection Requirements
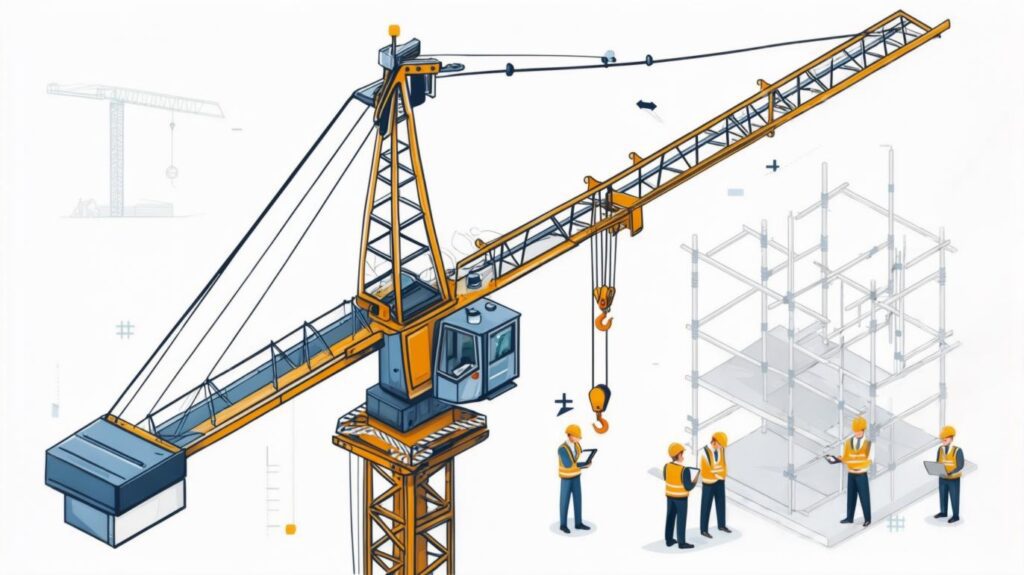
1. Shift Inspections: The First Line of Defense
Under 29 CFR 1926.1412(d), a competent person—one capable of identifying hazards—must begin a visual inspection prior to each shift. This “walking the blocks” routine checks for:
- Control Mechanisms: Maladjustments or sticky levers
- Drive Components: Excessive wear, contamination by lubricants or debris
- Pressurized Lines: Leaks or deterioration in hoses and fittings
- Hydraulic Systems: Proper fluid levels and absence of contamination
- Structural Components: Cracks, deformities, or corrosion in booms and frames OSHA
This simple yet vital step often catches red-flag issues before they escalate into costly downtime or, worse, accidents.
2. Monthly Inspections: Deeper Dive
Each calendar month, inspections take on a more thorough scope under 29 CFR 1926.1412(e). While still performed by a competent person, monthly checks extend beyond a visual sweep to include:
- Monitoring deficiencies noted in the annual inspection
- Wire rope evaluations—no more than six broken wires in one lay OSHA
- Brake performance, limit switch function, and load-block integrity
- Detailed look at control panels, wiring, and emergency stops
All findings must be documented (per 1926.1412(e)(3)) and made available to inspectors.
A Personal Note: On a recent project remodeling a downtown historic site, our team’s monthly inspection flagged a minor hydraulic leak that had gone unnoticed. Addressing it early saved us from replacing a $5,000 cylinder—and prevented potential environmental hazards.
3. Annual (Comprehensive) Inspections: The Gold Standard
At least every 12 months, cranes & derricks require a deep, documented review by a qualified person—someone with recognized training or experience in crane systems (1926.1401) OSHA. These inspections cover:
- Structural Integrity: Nondestructive testing of welds and key components
- Mechanical Systems: Verification of gearboxes, wire ropes, and brake hardware
- Electrical Controls: Inspection of relays, transformers, and pendant stations
- Load Tests: Where applicable, confirming rated load capacity per manufacturer specs
- Complete Documentation: Including deficiencies and corrective actions OSHA
OSHA’s letter of interpretation clarifies the annual inspection must occur on or before the anniversary date of the last inspection, not merely by month-end OSHA.
Building the Right Crane Inspection Checklist
When it comes to crane inspection requirements, many companies focus only on ticking boxes without truly understanding the purpose behind each step. From my experience managing lifting operations on construction sites, I’ve learned that having a proper checklist not only meets OSHA and compliance standards, but also builds a safety-first mindset among the team. One of the biggest mistakes I’ve seen is treating daily and monthly inspections as routine chores, rather than powerful tools that prevent equipment failures and serious accidents.
To make your inspection process effective, it’s essential to include both visual and operational checks. A good checklist will guide your team through verifying all mechanical components, checking electrical systems, and ensuring safety devices are working properly. In fact, including hydraulic and pneumatic systems can save hours of downtime later. When these elements are consistently examined, it becomes much easier to identify potential issues before they become costly problems. Personally, I’ve seen teams avoid major delays just by spotting small leaks early during pre-shift inspections.
Another important element often overlooked is documentation review. Especially when following third party crane inspection requirements, maintaining clear and detailed records makes audits smooth and stress-free. I recommend standardizing this process—it not only helps your crew understand what to look for, but it also ensures every part of the crane gets regular attention, from structural examination to load testing. Following a well-structured routine reinforces a culture of accountability and helps meet both internal and regulatory expectations.
Finally, embedding this detailed checklist into your company’s safety program is not just smart—it’s essential. It shows your commitment to your crew’s well-being and the reliability of your lifting equipment. By adhering to these steps, you’re not just avoiding malfunctions, you’re creating a safer work environment. That’s the real power behind understanding crane inspection requirements the right way.
How Often Should You Inspect a Crane?
When it comes to crane inspection requirements, frequency plays a big role in staying compliant and safe on site. Based on my experience working closely with heavy equipment operators and safety officers, one of the most overlooked elements isn’t the inspection itself—it’s the intervals and consistency. According to OSHA and manufacturer guidelines, all active cranes need to be inspected at least once a year, but that’s just the bare minimum. Depending on the usage—especially in environments classified as normal, heavy, or severe service—those inspection intervals can shift quickly to quarterly, bimonthly, or even daily.
In most of the projects I’ve handled, we break down inspections into frequent and periodic. Frequent inspections are visual and should be done daily. They involve checking hooks, hoist chains, operating mechanisms, and the components of air or hydraulic systems. OSHA even recommends quick testing before every shift. On the other hand, monthly checks need a certified professional. I always ensure that our crane inspector signs and dates the written records, which serve as valuable documentation—especially during an OSHA investigation or incident review.
Periodic inspections dig deeper. We look out for loose bolts, cracked sheaves, damaged locking devices, and wear on the braking system. These inspections also include checking wind indicators, load indicators, gasoline or electric power plants, and electrical wiring. It’s not just about finding what’s broken—it’s about preventing potential failures. These checks are vital in meeting both OSHA requirements and third party crane inspection requirements, which often come into play for larger projects or clients with high liability concerns.
In high-risk areas, especially when cranes are working non-stop or lifting extreme loads, we follow a strict compliance routine. The comprehensive nature of inspections—paired with properly maintained records—not only ensures safety but also protects us from legal and financial liability. Trust me, in this industry, solid procedures backed by real evidence can make or break your credibility.
Who Is Qualified to Inspect a Crane?
When it comes to crane inspection requirements, the safety of your job site depends heavily on who is performing the checks. From my own experience working around heavy equipment, I’ve seen how critical it is to choose the right individual for the job. A proper inspection isn’t just about ticking boxes—it’s about having a competent, hands-on expert who knows how to spot hazards before they become real problems. According to the industry standard, especially those set by OSHA, only a person who is capable of thoroughly examining the crane and is authorized to make safety decisions should be doing this.
Whether it’s someone from within the team or through third-party crane inspection requirements, it’s essential that the employee or company conducting the inspection is well-qualified. In many cases, a third-party inspector is preferred for unbiased assessments. These professionals are often appointed by the employer and must be able to identify defective components, maladjustments, or even deformations in the structure. They should be skilled enough to understand how each part affects the crane’s function as a whole.
From what I’ve seen on industrial sites, inspections done by a less-experienced person often miss critical issues—something you can’t afford when heavy lifting is involved. A trained crane inspector has the technical eye to catch what others might overlook. More importantly, they’re held to the same high bar whether they’re part of the internal crew or brought in under third-party crane inspection requirements.
When Should Crane Inspections Be Done?
Crane inspection requirements are essential to ensuring that cranes operate safely and effectively. Frequent inspections are necessary, with intervals typically ranging from daily to monthly. These inspections focus on critical operating mechanisms, like the hydraulic system, hoist chains, and hooks, making sure everything is functioning as it should. It’s not just about checking the parts, but also ensuring they are in good condition and working properly.
Periodic inspections are carried out at regular intervals, such as bimonthly, quarterly, or annually, depending on how often the crane is used. These checks are more in-depth, focusing on overall wear and tear. You’ll find that parts like sprockets, sheaves, rivets, and brakes are closely examined to prevent any malfunction that could cause an accident.
Moreover, don’t forget about the initial inspections. Every new crane, or one that’s been altered, needs to be thoroughly checked before it’s put into use. Also, make sure to perform comprehensive inspections every four years for cranes, whether they’re new, used, or altered. This ensures their longevity and safe operation over time. Additionally, it’s critical that annual inspections are conducted on or before the anniversary date of the previous inspection, ensuring that your crane continues to meet safety standards.
Frequent Crane Inspections
Regular inspections are essential to maintain the safety and efficiency of cranes, with some occurring on a daily to monthly basis. This ensures any defects or operational issues are caught early, keeping the crane in top condition. Frequent inspections help identify problems during operation hours and between scheduled inspections, ensuring no surprise breakdowns. As a part of the inspection routine, it’s important to check all functional operating mechanisms for any signs of maladjustment that could interfere with proper operation or cause excessive wear on critical components.
Additionally, air and hydraulic systems must be carefully checked for any signs of deterioration or leakage in parts like lines, tanks, valves, and drain pumps. Hooks should be examined for deformation or cracks to avoid dangerous failures. Hoist chains require inspection, particularly their end connections, to ensure there’s no excessive wear, twist, distorted links, or stretch beyond what the manufacturer recommends. For the rope, reeving should be checked to ensure it complies with the manufacturer’s instructions, ensuring smooth operation without any risk of failure.
Streamlining Compliance: Tips & Best Practices
- Leverage Checklists & Software
Use digital inspection platforms that timestamp entries, attach photos, and auto-generate follow-up tasks. This cuts down manual paperwork and ensures no item is overlooked. - Train & Certify Your Team
Invest in qualified-person training (see §1926.1429 for inspector qualifications). A well-trained inspector reduces overlooked hazards and reinforces safety culture OSHA. - Integrate Internal Resources
Link to Crane Safety Tips: Best Practices on your site to guide operators through quick daily checks—boosting accountability and awareness. - Proactive Replacement
Monitor wire rope wear against removal-from-service criteria. Replacing a rope at 50% of wear capacity can be 30–40% less expensive than emergency change-out during a breakdown. - Coordinate with OEMs
For new or altered cranes, follow manufacturer-specified load tests (per ANSI B30.2). Recording OEM-approved procedures shields you during OSHA audits OSHA.
Conclusion
Meeting OSHA’s Crane Inspection Requirements isn’t just about avoiding fines—it’s about elevating site safety, protecting your team, and ensuring uninterrupted operations. By mastering shift, monthly, and annual inspections—and embedding a culture of continual vigilance—you transform compliance from a checkbox exercise into a strategic advantage.
Have you updated your crane inspection program this year? Share your experiences or questions in the comments below. Looking for deeper insights? Subscribe to our newsletter for exclusive safety checklists, expert webinars, and more. Let’s keep your cranes—and your crew—operating at peak safety!
For Mobile Crane rentals please contact us.